Construction and types of turbines

It's really two elements, a turbine and a compressor. It is a subassembly whereby we recover some of the energy from the exhaust gas leaving the engine. They drive the turbine wheel, which is connected to the compression wheel via the shaft. The supplied air is compressed in the compressor part and, when cooled in the intercooler, the intake manifold goes to the combustion chamber. At that time, the density increases, ie the mass of the charge supplied to the combustion chamber increases, so it is possible to burn more fuel-air mixture and thus increase the power of the engine.
Turbocharger construction

Hot side
Also called the exhaust side of the turbine. Due to the high temperatures, these elements must be made of materials with very high heat resistance. We have in mind both the housing and the wheel with the shaft. It is here that the energy released from the exhaust which drives the compressor is released.
Cold side
The compression side which consists of a wheel and housing and some of the "Baypas" bleed valve solutions. Through the rotational speed of the wheel, air is drawn in, which is then pushed through the compressor housing into the intercooler.
Middle body / bearing system
The turbocharger shaft is seated in the middle body in which the bearings are located. In most cases, these are plain bearings made of bronze alloy, but increasingly we find ceramic ball bearings that are characterized by lower mechanical resistance and high service life. Bearing in the vicinity of the turbine is exposed to high temperatures. Note that the oil that is responsible for the lubrication of the spinning system is also meant to cool the central body, so it is important that the quality and oil pressure are so important. As an additional cooling element some subassemblies (especially for gasoline engines) are equipped with cooling engine coolant.
Types of turbochargers
Turbocharger „Free float”
The solution most commonly found in the charging of engines of trucks and work machines. It is characterized by a lack of control valve, all exhaust gas leaving the engine goes directly to the turbine wheel. In this case, the supercharging pressure depends only on the size of the hot and cold side wheels.

Turbocharger with Wastegate
Turbochargers equipped with an exhaust valve have built-in recharge control devices. This device consists of a pneumatic actuator connected to the bleeder flap mounted in the turbine body. Thanks to the use of turbo valve can automatically limit the maximum recharge. The benefits of this solution include extended service life, faster recharge and the ability to set it up.

Turbocharger VNT/VTG
Currently the most common solution in diesel engines of passenger vehicles. Thanks to the variable geometry system in the turbine body, it is possible to make better use of the exhaust energy over the whole engine speed range. To further control the work of variable geometry in place of pneumatic valves, manufacturers increasingly use electronic control valves (SREA, REA). This eliminates the "turbo-hole" effect found in older engine designs. Substantially improved propulsion performance has been improved with increasingly stringent environmental standards.

Types of charging
Bi Turbo
It is a recharge based on the work of two independent turbochargers working in parallel. The solution is now found in larger capacity engines and V-series engines.

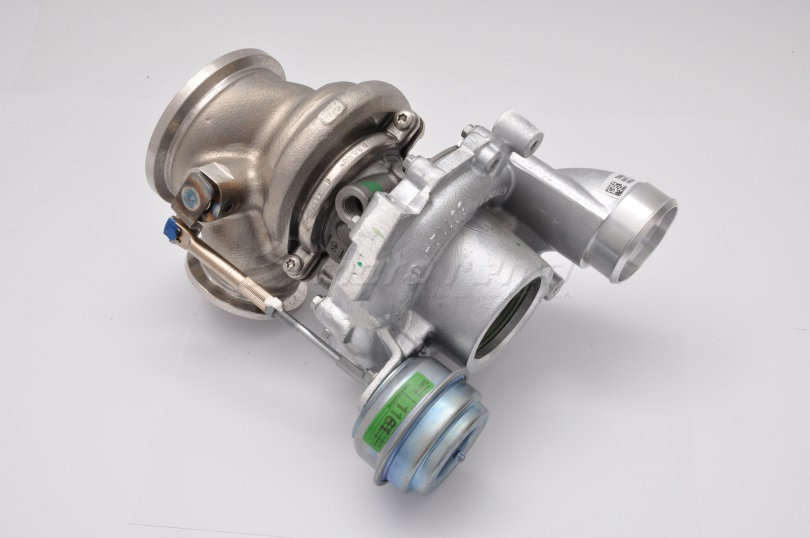
Twinturbo (R2S)
The arrangement of two different "small" and "large" turbochargers. The smaller is responsible for recharging in low engine speed ranges where the exhaust gas pressure is low. At full load through the respective exhaust valves, drive both turbines running in parallel.